Home ·
Email ·
List of Projects ·
Project Sites and Links ·
Articles ·
Robert Davis Biography
Filene Center II - Wolf Trap Farm Park for the Performing Arts
Vienna, Virginia
Summary of Physical Facilities
Location
The Wolf Trap Farm Park for the Performing Arts - the only national park
devoted to
the performing arts - consists of 117 acres of wooded rolling
countryside
just outside
Washington, DC in Vienna, Virginia.
History
The original Filene Center opened in 1971 and burned to the ground in
1982.
Filene Center II opened July 30, 1984.
Management
The theater was a gift to the U.S. government from the Wolf Trap
Foundation. The facilities
are managed by the U.S. Department of the Interior National Parks
Service.
Programming
is managed by the Wolf Trap Foundation.
Project Scope
Facilities include the 6700 seat auditorium with 2600 covered orchestra
seats, 1100 covered
balcony seats, and 3000 lawn seats, the stage and backstage facilities,
large rehearsal room,
administrative offices, dressing rooms, canteen, and miscellaneous
support
spaces.
Presentation Program
The house is a "road house", presenting opera, dance, symphony music,
Broadway tours,
popular music, and film. The Wolf Trap Foundation manages an opera
company, other
performing companies, and educational activities. These activities use
the adjacent performing
barns and occasionally perform in the Filene Center.
Costs
Rebuilding after the fire cost $20 million. The new facility is four
times larger backstage
than the original building. Some items such as foundations, site
work and
utilities were
salvaged and their reuse lowered rebuilding costs slightly compared to
what a new facility would cost.
Statistics (Stagehouse)
Proscenium opening: 70' wide by 35' feet high (45' for orchestra
shell).
Stage dimensions: Stage edge to house curtain 6', house curtain to back
wall 59', total depth 65'.
Center line to the stage left wall 50', center line to the stage right
locking rail 68', total width of stage house 118'.
Maximum batten trim: 95'.
Galleries: 1 fly gallery each stage left and right connected by
crossover gallery, two loading galleries stage right.
All galleries and grid are connected by an upstage right stair tower and
an upstage left personnel elevator.
The stage manager's position is downstage right.
Statistics (House)
Total capacity is 6700. 2600 covered orchestra seats, 1100 covered
balcony seats, and capacity for 3000 patrons uncovered on the lawn.
Orchestra pit elevator 10'X60' tapers from 38' to 60'. Pit extends
under stage apron 13'X68'. The pit
mechanism is jackscrews with the ability to stop and hold at any
elevation
between orchestra pit and stage.
Two enclosed, air conditioned control booths are provided in the
orchestra seating area. The house left
booth is for lighting and the house right booth is a spare. The house
sound mix location is in the orchestra
seating area house right. The sound mix location for lawn patrons is
located at the center rear of the
lawn area and is a complete independent mixing location.
The first two catwalks over the apron provide access to forestage
loft
block beams intended for attachment
of temporary lighting and sound equipment such as television lighting
battens, rock group lighting trusses,
and speaker clusters.
Statistics (Backstage at stage level)
Side stage Stage Left 48'X48'.
Upstage scenery storage 46'X168'.
Crossover is through the upstage scenery storage room.
Rehearsal room behind upstage scenery storage room is 56'X95' with 30'
clear height, skylights, and is
acoustically isolated from stage.
Statistics (Backstage below stage level)
Green room 32'X18', musicians lounge 30'X58' with direct access to
pit, 2
additional performers lounges, and
a large, efficient canteen.
Dressing rooms
Each with toilets, showers, and lavatories.
# |
Capacity |
Size |
2 |
1 |
7'X8' |
9 |
1 or 2 |
9'X10' |
3 |
Chorus |
22'X40' |
2 |
Quick change |
Quick change dressing rooms are located onstage.
Wardrobe room is 18'X29' with 2 washers, 2 dryers, and a double
sink.
Acoustical Shell
The acoustical shell ceiling and wall pieces store in the scenery
storage
areas. When stored the shell takes
up no space onstage. The shell is 70' wide by 45' high at the
proscenium
opening and 54' wide by 35' high at
the back. The rear wall is set 42' back from the edge of the permanent
stage. The shell carries a set of
permanent concert lights and has extra mounting pipes and circuits for
adding specials. The stage lighting
system is used to supplement the orchestra front lighting carried on the
shell. Double doors are
provided in the upstage and downstage towers of both side walls. Time
required to set or strike the shell
is less than three hours.
Rigging
104 single purchase counterweight sets with 80' long battens, each with
2000 pound capacity arbors and
compensating cables on 6" centers. 200,000 pounds of lead
counterweights
are available. Two 2000 pound
capacity electric winches with removable battens are located under the
light bridge. The locking rail is
duplicated at stage level and at the first fly gallery stage right.
House
curtain is manually operated from
stage right. A steel framed fire curtain is designed to resist severe
wind loads and may be left
closed all winter if desired.
Lighting
660 20-ampere circuits and 54 50-ampere circuits, totaling 714 dimmers.
This is a dimmer per circuit
system with an individual dimmer for each circuit. There is no patch
panel. Identical control consoles
are located onstage right and in the lighting control booth in the
orchestra. Each console location also
has complete control of 24 non-dims, houselights, 36 circuits of
worklights, parking lot lights, security
lighting, and site lighting. The light bridge is wired with permanent
circuits.
All other overhead
onstage circuits are terminated in portable drop boxes and can be
attached
to any batten, ladder, or boom
onstage. Stage lighting positions in the auditorium include two catwalks
over the apron, a far catwalk at the
followspot position, a balcony rail, and box boom galleries left and
right. On-stage lighting positions include
5 house borderlight pipes, 10 ladders, 10 booms, a footlight trough,
three
cyc pits, and the light bridge.
The followspot booth is enclosed and air conditioned. Fans prevent
condensation from accumulating
on the outside of the followspot window.
Instruments
86 |
10 degree ERS 1kW |
36 |
15 degree ERS 1kW |
134 |
25 degree ERS 1kW |
12 |
6x16 ERS 1kW |
124 |
6x12 ERS 1kW |
20 |
6x9 ERS 1kW |
12 |
6" Fresnel 750W |
90 |
8" Fresnel 1.5kW |
100 |
PAR64 1kW |
6 |
2-lamp cyc lite 2x1kW |
6 |
4-lamp cyc lite 4x1.5kW |
7 |
12-lamp 4-ckt PAR38 strip |
25 |
12-lamp 4-ckt PAR56 strip |
12 |
12-lamp 3-ckt PAR56 strip |
6 |
9-lamp 3-ckt EMD ground row |
10 |
12-lamp 3-ckt PAR64 1kW strip |
4 |
Xenon arc followspot 2kW |
 |
Music stands and stand lights |
Accessories include complete cable, hardware, iron, booms, sidearms,
ladders, hi-hats, barn doors,
striplight glass, two sets of color frames, bumpers, etc.
Available auxiliary power
Company switches upstage right, 3 at 400 amperes 3-phase 4-wire each.
(This totals 9 400 ampere legs).
In each of the four stage corners is a 100 ampere 3-phase 4-wire switch.
In each of the four stage
corners is a 36kW power panel with pin connector, household, and 208
volt
outlets for tools, effects,
worklights, welders, smoke machines, winches, etc.
Sound Systems
Bi-amped JBL speaker clusters are installed for the center cluster,
under-balcony, over-balcony, and for the
lawn seating. Side stacks are available. House clusters are delayed
digitally as appropriate. Input
lines and sub-mixes are split to three consoles, one for onstage monitor
speakers, one for the main house mix,
and one for the lawn mix. Input lines are also split for TV and record
production trucks at the stage door.
Portable equipment includes tape recorders, microphones, and
stands. A
hard-of-hearing system and translation
system are available. The hall uses electronic acoustical enhancements.
Complete monitor,
paging, and communications systems are installed. The stage monitor mix
location is downstage left and the
house sound rack room is in the basement directly below the monitor mix
location.
Closed Circuit Video
A closed circuit video system for production and security includes
remote
control balcony rail and
onstage cameras for stage monitoring, a conductor camera, and
distribution
of stage lighting data
displays to portable and permanent house video monitors. Patch bays are
provided for over 100 house video
circuits serving security cameras, security monitor stations, and
production needs.
Soft Goods
Black velour pieces with no fullness available from the house include 8
borders, 16 legs, 2 travelers, and 2
split blackout drops. Other house goods include one each, black scrim,
blue scrim, white scrim, muslin reflector
drop, plastic cyclorama, and 2 hard black velour portal legs on
travelers.
Loading doors
Two loading doors for semi-trailers are located in the upstage right
corner of the upstage scenery storage
room, each has a 4' high dock.
Stage Flooring
The stage floor is made of two inch thick solid edge grain fir planks
supported on a grid of two inch thick
resilient neoprene pads. The deflection of the floor under the
weight of
dancers is not limited. Dancers
feel the floor to be very soft. Under heavier loads the floor
deflection
is limited by solid blocks, preventing
damage to the floor from excess deflection. Traps are not provided but
can be cut when needed. The resilient
flooring extends onto the orchestra pit lift platform. Three cyclorama
pits and ratholes for microphone cables are
provided.
House Curtain
The house curtain is a weave of wool yarns that were hand spun and hand
dyed with organic dyes in Swaziland.
The curtain design is large plain vertical panels of muted colors.
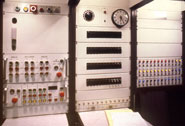
Electrical equipment is durable and modular for repair and replacement
over a life expectancy of many decades.
Shown here are controls for the orchestra pit lift, light bridge, fire
curtain, orchestra shell ceiling, light ladders,
worklights, parking lot lights, and miscellaneous other controls.
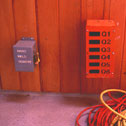
Electrical boxes are color-coded by function. The boxes here are a data
box and a Q-light box.
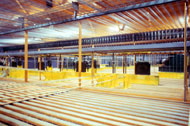
The gridiron is efficient and safe. Large winches are located here for
the traveling lighting ladders, the orchestra
shell ceiling, the light bridge, and the fire curtain. The 104
single-purchase counterweight rigging sets are all identical.
The predictability of having all sets identical makes planning a
load-in simpler. The 100-foot high grid can
be accessed with normal stairs and with a motorized personnel lift.
Home ·
List of Projects
|